Stop These Welding Defects With Des Moines, IA Portable Welder
Porosity: Porosity refers to gas pockets that form during the solidification of the weld metal. These pockets can weaken the weld and make it susceptible to failure.
Cracking: Cracking is another common welding defect when the weld metal cools too quickly or when there is too much stress on the weld. Cracks help weaken the weld and make it susceptible to failure.
Distortion: Distortion is a change in the shape of the welded material that occurs because of the heat of the welding process. Distortion will be light and helps affect the fit of the welded components.
Welding is critical in various applications, from construction and manufacturing to repair and maintenance. Yet, welding helps be a complex process, and if not done correctly, it leads to defects. Using experts in welding like McMahan Industrial Services helps avoid double jobs and defects.
Common Welding Defects
Some of the most common welding defects include porosity, cracking, and distortion.
Porosity
Porosity refers to gas pockets that form during the solidification of the weld metal. These pockets can weaken the weld and make it susceptible to failure. Several factors can contribute to porosity, including:
Improper shielding gas: The shielding gas protects the weld metal from contamination from the atmosphere. If the shielding gas is not flowing or is contaminated, it leads to porosity.
Moisture: Moisture on the base or filler metal helps cause porosity.
Excessive welding speed: If the welding speed is too fast, the weld metal will not have time to solidify, which leads to porosity.
Cracking
Cracking is another common welding defect when the weld metal cools too or when there is too much stress on the weld. Cracks help weaken the weld and make it susceptible to failure. Several factors can contribute to cracking, including:
Improper preheat: The preheat temperature is the temperature at which the base metal is heated before welding. If the preheat temperature is too low, it leads to cracking.
Improper cooling rate: The cooling rate is when the weld metal cools after welding. If the cooling rate is too fast, it leads to cracking.
Excessive stress: Excessive stress on the weld leads to cracking. This can be caused by improper joint design or improper weld positioning.
Distortion
Distortion is a change in the shape of the welded material that occurs because of the heat of the welding process. Distortion can affect the fit of the welded components. There are many factors contributing to distortion, including:
The thickness of the base metal: Thicker base metal is more susceptible to distortion than thinner base metal.
The type of weld: Some welds are more susceptible to distortion than others. For example, butt welds are more vulnerable to distortion than fillet welds.
The welding sequence: The welding sequence is the order in which the welds are made. A carefully planned welding sequence helps to cut distortion.
About McMahan Industrial Services
McMahan Industrial Services is a leading provider of portable welding services in Des Moines, IA. Our experienced welders handle various welding projects, from simple repairs to complex fabrication.
Welding defects can be a severe problem, and taking steps to prevent them is essential. If you are tired of searching for a portable welder in Des Moines, IA, Contact Us Today to meet your welder needs and let us exceed your expectations!
Also, browse our project gallery for an idea of projects we undertake or check Google reviews.
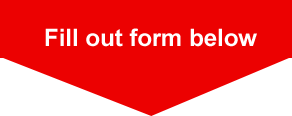