Welding large diameter pipes takes special techniques and equipment to make sure the welds are strong and high-quality. One popular method for this is Gas Metal Arc Welding (GMAW). It works well because it has high deposition rates and creates strong welds.
But, if the area being welded isn't properly shielded, you can run into problems like porosity, which creates defects and weakens the pipe.
To help avoid mistakes like porosity, automated orbital welding can be really useful. This method uses computer-controlled welding torches to get the job done right.
For successful pipe welding projects, it's important to have a well-planned schedule. This should include thorough pipe inspections and working with certified welders from McMahan Industrial Services.
By understanding these techniques and considerations, you can achieve reliable and efficient pipe welding results.
Pipe Welding Techniques
When welding large diameter pipes, picking the right welding technique is crucial since it affects the quality and strength of the weld, as well as the efficiency of the job.
At McMahan Industrial Services, we often use the Gas Metal Arc Welding (GMAW) technique for these projects. It's a popular option because it allows for high deposition rates and creates strong, high-quality welds.
GMAW feeds a continuous wire and uses an inert gas to shield the weld area. This shielding is crucial because it protects the weld from atmospheric gases, which can lead to defects like porosity.
Porosity Issues in Welds
Porosity is a common problem in welds, especially in large pipes. It happens when gases from the atmosphere get into the weld pool, creating defects that weaken the pipe and can be unsafe.
Porosity might occur for several reasons, such as dirty weld areas, using the wrong shielding gas, or not using the right welding technique.
At McMahan Industrial Services, we focus on reducing the risk of porosity by ensuring that the weld area is clean and dry, using the right shielding gas, and sticking to consistent welding techniques.
We also believe in regular inspection and testing to catch any porosity issues before they become serious problems.
Automated Orbital Welding Benefits
Automated orbital welding is a great way to reduce mistakes like porosity in welds. When welders use proper techniques and inspections, they can take advantage of advanced technologies to work more efficiently and improve the quality of their welds.
Automated orbital welding systems use computer-controlled welding torches that create consistent, high-quality welds. This reduces the chances of human error.
Plus, these systems can be programmed to weld pipes of different sizes and thicknesses, making them perfect for large projects.
By choosing automated orbital welding, pipe welders can boost productivity, cut costs, and enhance the overall quality of their work. This leads to safer and more reliable pipelines.
Schedule Expert Pipe Welding
Every successful pipe welding project needs a well-planned schedule to ensure that everyone involved is on the same page and that the project stays on track.
A good schedule helps avoid delays, cut costs, and keep the work environment safe.
That's why it's essential to work with a certified welder who has the right skills and experience in pipe welding.
Before starting the welding process, it's also important to conduct a thorough pipe inspection to catch any potential issues.
Contact Us Today to meet your welder needs and let us exceed your expectations! Also, browse our project gallery for an idea of projects we undertake or check Google reviews.
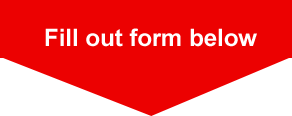