As a pipe welder at McMahan Industrial Services in Minneapolis, MN, getting a grip on pipe welding techniques is crucial for beginners. You need to understand the basics of pipe materials, how to prevent corrosion, and specialized welding techniques.
Different pipe materials, like stainless steel and copper, require their own unique welding approaches. Corrosion can weaken pipe structures in humid environments, so it's essential to know what causes it to prevent it.
Types of Pipe Materials
When it comes to pipe welding, the type of pipe material you're working with makes all the difference. At McMahan Industrial Services, we know that understanding the unique characteristics of different pipe materials is key to achieving a strong, leak-tight joint.
Pipe materials vary in terms of their strength, resistance to corrosion, and how well they can be welded. Pipe grades, such as API 5L, ASTM A106, and ASTM A53, are categorized based on their material strength, which affects the welding process. For example, high-strength pipes require specialized welding techniques and equipment to prevent damage.
By knowing the properties of different pipe materials, welders can choose the right welding technique, filler metal, and heat treatment to ensure a strong and reliable joint.
At McMahan Industrial Services, we emphasize the importance of selecting the right pipe material and using proper welding techniques to maintain the integrity of piping systems.
Corrosion in Humid Environments
Corrosion in humid environments is a major issue that pipe welders at McMahan Industrial Services need to tackle head-on.
When moisture is present, it accelerates the degradation of metal surfaces, leading to rust and corrosion. In coastal areas, the combination of saltwater and high humidity creates the perfect storm for corrosion to occur. Temperature, humidity, and air pollution are all environmental factors that contribute to corrosion.
In humid environments, corrosion can happen rapidly, causing structural weaknesses and even failures. That's why understanding what causes corrosion is crucial for pipe welders. By knowing the risks, they can take steps to prevent corrosion and protect pipes.
MIG Welding for Stainless
When it comes to MIG welding stainless steel pipes, it's crucial to protect the weld area from oxygen and water vapor.
These elements can cause porosity and oxidation, which can ruin your weld. To prevent this, we use a shielding gas, typically a mix of argon and helium, to displace the air around the weld area. This gas also helps to improve weld penetration and reduce spatter.
At McMahan Industrial Services, we know that maintaining a consistent welding speed is key to achieving a smooth, even weld. If you weld too slowly, you can end up with a lack of fusion, while welding too quickly can cause porosity. By controlling your welding speed and using the right shielding gas, even beginners can produce high-quality welds on stainless steel pipes.
Book Your Expert Welding for Copper
When working with copper pipes, specialized welding techniques are crucial to ensure strong and reliable joints. At McMahan Industrial Services, we understand that copper's high thermal conductivity and corrosion resistance present unique challenges.
In addition to quality, Copper Aesthetics play a significant role, especially in applications like plumbing fixtures and architectural features where visually appealing welds are often a requirement.
Contact Us Today to meet your welder needs and let us exceed your expectations! Also, browse our project gallery for an idea of projects we undertake or check Google reviews.
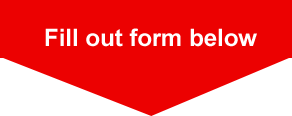