Power generation equipment repair welding in Waterloo, IA is a complex process that requires specialized expertise. At McMahan Industrial Services, we understand the unique challenges involved.
For instance, we know that high-temperature alloys like Inconel and Haynes are needed to withstand extremely high temperatures. We're also aware that corrosion in boiler tubes can lead to tube failure, repairs, and downtime, so we identify the root causes to prevent these issues.
Our team uses micro-welding to join intricate components, ensuring joint integrity in harsh conditions. We also employ specialized welding techniques to repair turbine blades, maintaining their efficiency and reliability.
High-Temperature Alloy Expertise
High-temperature alloys, like Inconel and Haynes, are the go-to choice for power generation equipment at McMahan Industrial Services because they can withstand extremely high temperatures without breaking down.
When picking the right alloy, it's crucial to consider the specific demands of the job. Thermal fatigue, a major concern in power generation, can cause equipment to fail prematurely if it's not addressed. By selecting the right alloy, our engineers can reduce the risk of thermal fatigue and ensure that our equipment is reliable and efficient.
At McMahan Industrial Services, we know that a deep understanding of high-temperature alloys is vital for making informed decisions about alloy selection. This expertise helps us reduce downtime and extend the lifespan of power generation equipment.
Corrosion in Boiler Tubes
Boiler tubes are super vulnerable to corrosion because of the extreme conditions inside power generation equipment. We're talking high-speed steam and water flowing at scorching temperatures! This corrosion can lead to tube failure, which means costly repairs and downtime.
To prevent this, you need to understand how corrosion works.
At McMahan Industrial Services, we know there are several ways corrosion can occur in boiler tubes, including oxidation, pitting, and crevice corrosion. These mechanisms can be influenced by factors like water quality, temperature, and flow rates.
Micro-Welding for Precision Joints
In power generation equipment, precision joints are crucial for maintaining the system's integrity.
McMahan Industrial Services has found that micro-welding is an excellent technique for joining these intricate components. This process involves precise control over the welding parameters, ensuring the joint's integrity is preserved.
By using micro-welding, manufacturers and repair technicians can create strong, reliable joints that can withstand the harsh operating conditions of power generation equipment. This technique is especially useful in applications where traditional welding methods aren't feasible due to space or accessibility constraints.
Welding for Turbine Blades
Turbine blades are incredibly complex and delicate parts that are subjected to intense heat and mechanical stress. To repair them, specialized welding techniques are required to maintain their unique shape and structure.
At McMahan Industrial Services, our skilled welders understand that even the slightest deviation in blade geometry can significantly impact turbine efficiency and overall power generation.
When repairing turbine blades, our expert welders carefully consider crucial factors such as heat input, weld penetration, and residual stress to ensure that the blade is restored to its original specifications. By utilizing advanced welding techniques and materials, we can make repairs without compromising the blade's design integrity.
Contact Us Today to meet your welder needs and let us exceed your expectations! Also, browse our project gallery for an idea of projects we undertake or check Google reviews.
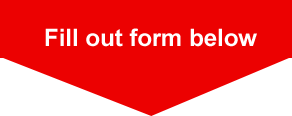