If you're a welder in Des Moines, IA, fixing weld cracks starts with figuring out what caused them in the first place.
Common problems include using the wrong welding techniques, having a poor joint design, not prepping the metal properly, and welding at too high temperatures.
When joints aren't set up right—like if they don't fit well or if they're dirty—it can lead to cracks.
Using the right shielding gas is really important, too, since it protects the arc and molten metal from the air.
Your welding technique matters as well; keeping a stable arc helps control the temperature and lowers the chance of porosity.
At McMahan Industrial Services, we believe that analyzing the welding process thoroughly is key to finding effective solutions.
Common Causes of Cracking
Weld cracking can happen for a bunch of reasons, like using the wrong welding techniques, having a poor joint design, or not preparing the metal properly before welding.
-
These issues can create leftover stresses and material problems.
-
One major reason for cracking is when the welding temperature is too high, which can wear the metal out and cause cracks to form.
-
To avoid cracking, it's important to use the right welding techniques.
-
This means keeping a steady welding temperature and properly preparing the metal beforehand to reduce those leftover stresses.
Inadequate Joint Preparation
One of the most important things that can cause weld cracking is inadequate joint preparation.
-
Proper joint preparation is essential for a strong and reliable weld.
-
If the surface is rough, it can create stress points that lead to cracks.
-
To avoid these issues, it's crucial to clean and degrease the joint area thoroughly and make sure the joint is properly machined and fitted.
-
Using the right welding process and technique can also help reduce the risk of weld cracking.
-
By following these steps, welders can ensure a strong and reliable weld.
-
Proper joint preparation is a key step in preventing weld cracking.
Proper Shielding Gas Usage
Using the right shielding gas is really important to prevent weld cracking. It protects the arc and molten metal from harmful gases in the air that can cause problems like porosity and cracking.
To make sure the shielding works well, it's crucial to keep the gas flow rates just right. These rates change depending on the welding method, the thickness of the material, and the type of joint. Generally, flow rates should be between 20 and 60 cubic feet per hour.
Another key factor is the purity of the gas. For most welding jobs, you should aim for a purity level of at least 99.99%.
Using high-quality shielding gases and keeping the flow rates correct can significantly lower the chance of weld cracking.
Book Your Mobile Welder Today
Most welding cracks happen because of a mix of reasons, but a lot of them come from poor technique. That's why it's super important to take a close look at how you weld and improve your skills to lower the chance of cracks.
Contact Us Today to meet your welder needs and let us exceed your expectations! Also, browse our project gallery for an idea of projects we undertake or check Google reviews.
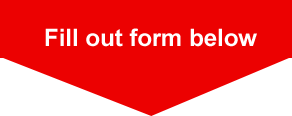